Project---Split cable pull linkage
- raygreenwood
- Posts: 11907
- Joined: Wed Jan 22, 2003 12:01 am
These are verysimilar to the pulleys on water cooled rabbits and golfs.
I have one I am playing with with my "bullet" style plateless TB that is a crude version of what I will describe below.
The thing to think about that I did not see mention of in this thread:......if you bore several different center shaft holes...eccentrically....off center....as well as several different cable mounting holes......it is quite easy to have a huge number of opening ratios...per mm of cable pull.
If you want to see the "parent" of this idea...simply look at "nautilus" excercise equipment. It is an eccentric "capstan". Turn diameter ratios can be adjusted by changing the relationship of the center bore and the mounting point for the chain/cable.....with reference to the length of the elliptical curve around the outside where the chain/cable runs.
Tougher to make....but maybe not.
The cable end could simply be a small heim joint... mounted to the disc on a steel pin with and E-clip. How far from the center this "pin" is mounted...governs the turn speed ratio.
Mounting the cable end closer to the center of the disc is quicker rotation speed......but shorter total stroke length in degrees of rotation.
Mounting the cable end closer to the outside edge is slower rotation speed but longer total stroke length in degrees of rotation.
You should also haveone dead center and several off-center mounting holes for the actual throttle shaft boss..........so.......
In operation ...you could have the cable intersect close to the center of the disc for that quick rotation speed.......but then mount the throttle shaft in one of the off center holes...opposite eccentrically to lengthen the stroke.....so you can get the best of both worlds. Totally adjustable.
The wire guide itself...instead of being a groove...can be a series of pegs with simple delrin roller chain bearings slipped over them.....to put in any holes you want to vary the diameter of the rotaion.
So to recap...you have a disc. (1) series of holes near the center ring for throttle shaft. One dead center..several eccentrically around in a spiral coming out from that. Maybe 5-6 choices. (
2) A series of holes for the cable heim joint mount pins. Some close to the outside edge of the disc....some toward the center....again descending from outside to the inside in a spiral arrangement. Maybe 10-12 choices total.
(3) several series of smaller holes...in complete circular rings...for the cable guide pins...maybe 4 rings of holes with ring diameter descending in diameter from the outside of the disc in.....maybe 1o pins on the outer...7 on the next......4 on the next...etc.
You could build this on a drill press. It would be incredibly adjustable.....and would solve many problems with improper TB sizing versus pedal stroke versus TPS stroke on plenum systems. Just some thoughts. Ray
I have one I am playing with with my "bullet" style plateless TB that is a crude version of what I will describe below.
The thing to think about that I did not see mention of in this thread:......if you bore several different center shaft holes...eccentrically....off center....as well as several different cable mounting holes......it is quite easy to have a huge number of opening ratios...per mm of cable pull.
If you want to see the "parent" of this idea...simply look at "nautilus" excercise equipment. It is an eccentric "capstan". Turn diameter ratios can be adjusted by changing the relationship of the center bore and the mounting point for the chain/cable.....with reference to the length of the elliptical curve around the outside where the chain/cable runs.
Tougher to make....but maybe not.
The cable end could simply be a small heim joint... mounted to the disc on a steel pin with and E-clip. How far from the center this "pin" is mounted...governs the turn speed ratio.
Mounting the cable end closer to the center of the disc is quicker rotation speed......but shorter total stroke length in degrees of rotation.
Mounting the cable end closer to the outside edge is slower rotation speed but longer total stroke length in degrees of rotation.
You should also haveone dead center and several off-center mounting holes for the actual throttle shaft boss..........so.......
In operation ...you could have the cable intersect close to the center of the disc for that quick rotation speed.......but then mount the throttle shaft in one of the off center holes...opposite eccentrically to lengthen the stroke.....so you can get the best of both worlds. Totally adjustable.
The wire guide itself...instead of being a groove...can be a series of pegs with simple delrin roller chain bearings slipped over them.....to put in any holes you want to vary the diameter of the rotaion.
So to recap...you have a disc. (1) series of holes near the center ring for throttle shaft. One dead center..several eccentrically around in a spiral coming out from that. Maybe 5-6 choices. (
2) A series of holes for the cable heim joint mount pins. Some close to the outside edge of the disc....some toward the center....again descending from outside to the inside in a spiral arrangement. Maybe 10-12 choices total.
(3) several series of smaller holes...in complete circular rings...for the cable guide pins...maybe 4 rings of holes with ring diameter descending in diameter from the outside of the disc in.....maybe 1o pins on the outer...7 on the next......4 on the next...etc.
You could build this on a drill press. It would be incredibly adjustable.....and would solve many problems with improper TB sizing versus pedal stroke versus TPS stroke on plenum systems. Just some thoughts. Ray
- Piledriver
- Moderator
- Posts: 22771
- Joined: Sat Feb 16, 2002 12:01 am

Remember, you need the sheathed cables so the sync doesn't change with motor temp variations/size changes.
Addendum to Newtons first law:
zero vehicles on jackstands, square gets a fresh 090 and 1911, cabby gets a blower.
EZ3.6 Vanagon after that.(mounted, needs everything finished) then Creamsicle.
zero vehicles on jackstands, square gets a fresh 090 and 1911, cabby gets a blower.
EZ3.6 Vanagon after that.(mounted, needs everything finished) then Creamsicle.
-
- Posts: 57
- Joined: Fri Jan 11, 2008 9:50 am
- Piledriver
- Moderator
- Posts: 22771
- Joined: Sat Feb 16, 2002 12:01 am
(I'm assuming you mean Slowtwitches setup, mine uses a linear slide/splitter and very long carb cables, on a Bug I'd probably put (maybe bolt) the splitter up on the trans...)westcoast-paul wrote:am i missing something, or does that cable turn 90 degrees out of the fan shroud? How did you handle that?
interesting setup
I'll guess it wraps around another pulley on a common shaft to the ones that go to the carbs and TPS.
I don't think it's actually connected in the pictures IIRC, so easy to get confused.
Addendum to Newtons first law:
zero vehicles on jackstands, square gets a fresh 090 and 1911, cabby gets a blower.
EZ3.6 Vanagon after that.(mounted, needs everything finished) then Creamsicle.
zero vehicles on jackstands, square gets a fresh 090 and 1911, cabby gets a blower.
EZ3.6 Vanagon after that.(mounted, needs everything finished) then Creamsicle.
- slowtwitch
- Posts: 533
- Joined: Mon Nov 08, 2004 9:38 am
- slowtwitch
- Posts: 533
- Joined: Mon Nov 08, 2004 9:38 am
Well, I finally got my camera back and took some pics of my modified linkage setup. It still needs a little fine tuning, but, seems to be working nicely.
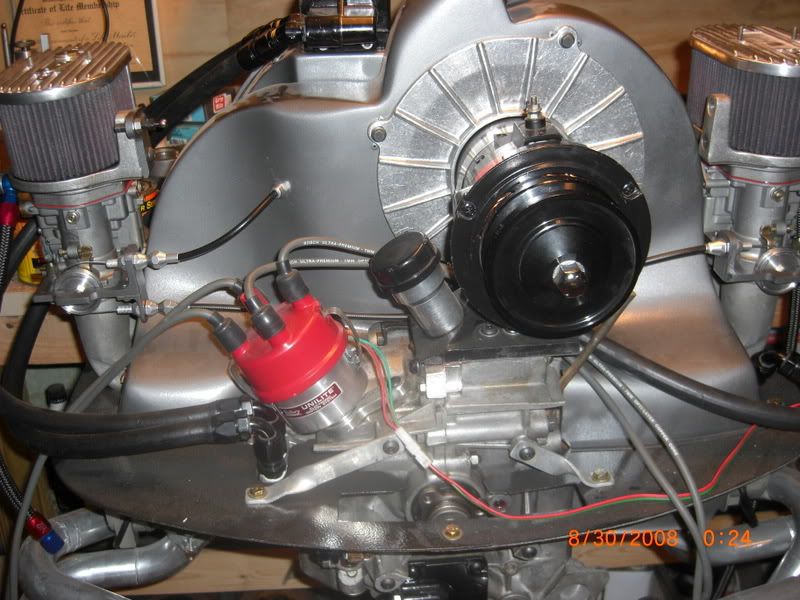
a closer look....Although, it works pretty freely, I may still go a bit bigger on the pulleys (it was the only stock I had). Gawd, that hex bar stuff is ugly
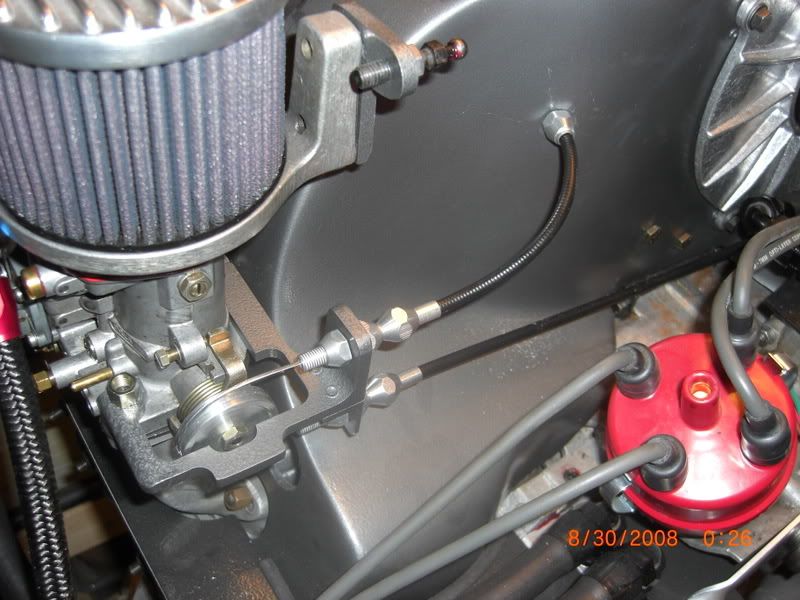
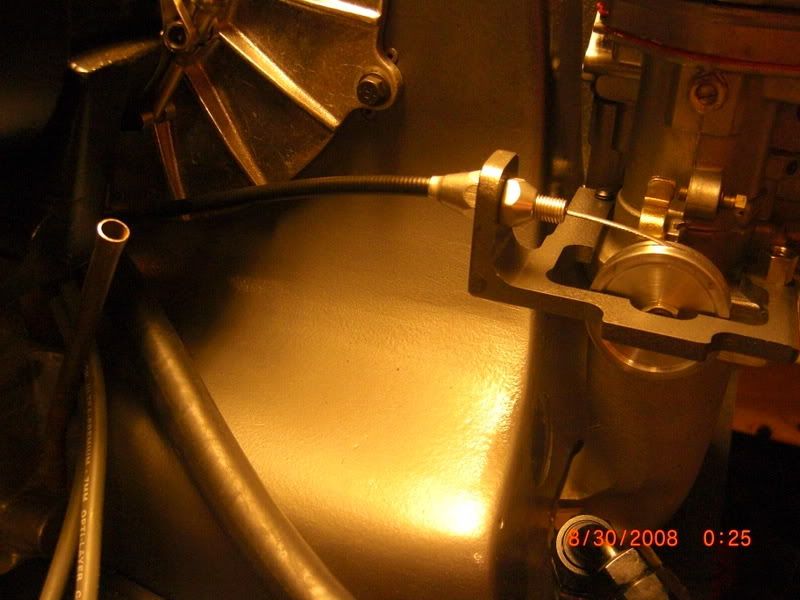
and the front side, I may change this out, with one that has a bend in it. We'll see when it comes time to install this thing

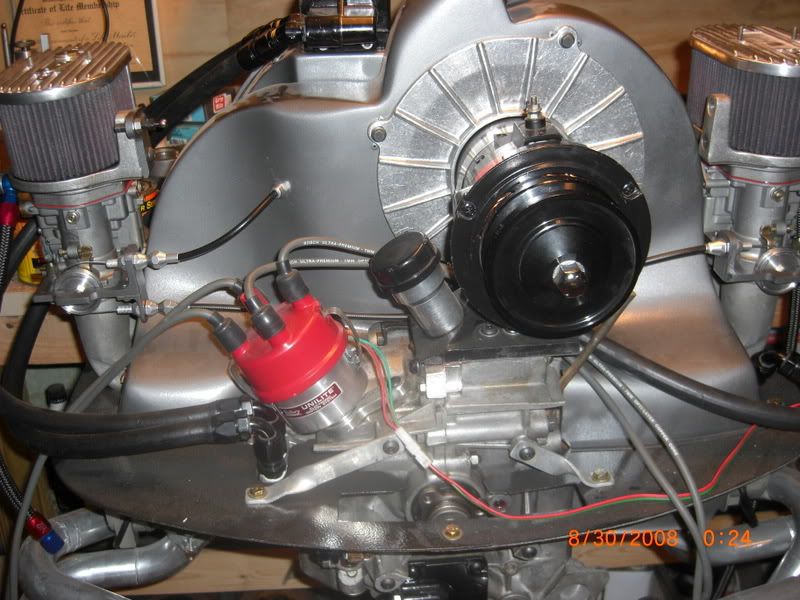
a closer look....Although, it works pretty freely, I may still go a bit bigger on the pulleys (it was the only stock I had). Gawd, that hex bar stuff is ugly

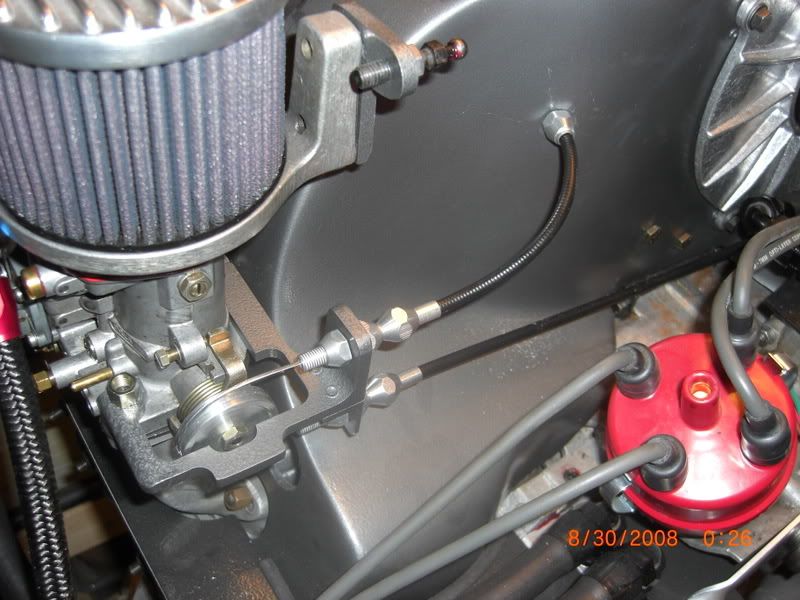
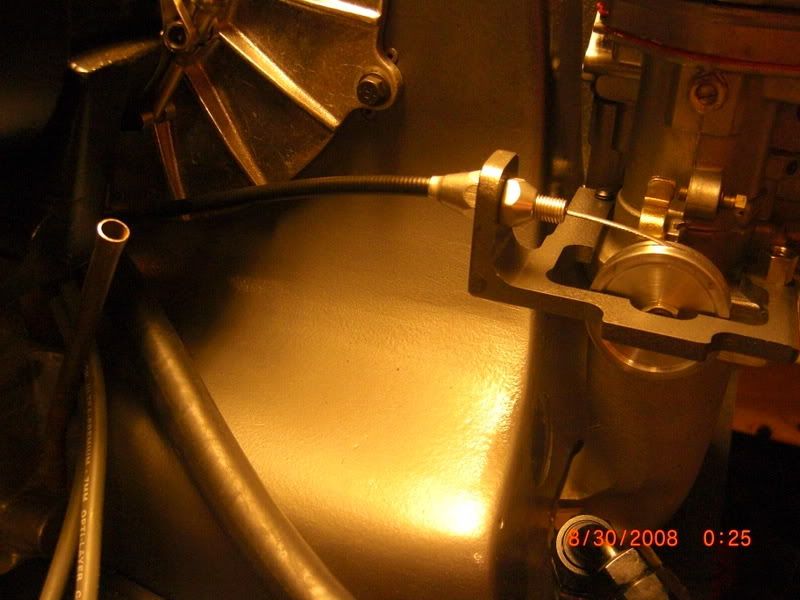
and the front side, I may change this out, with one that has a bend in it. We'll see when it comes time to install this thing

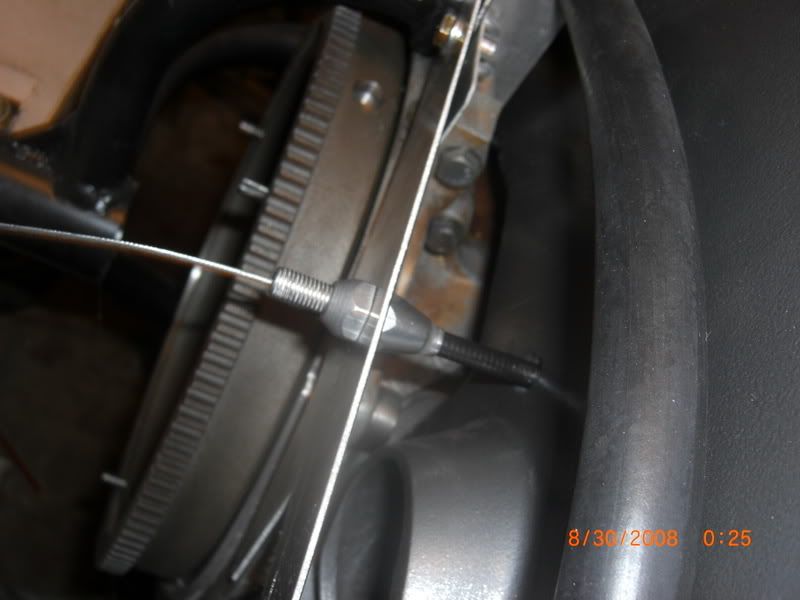

pete
- Piledriver
- Moderator
- Posts: 22771
- Joined: Sat Feb 16, 2002 12:01 am
Sweet! Totally Sanitary.
As long as the carb-to-carb cable/sheath isn't stretched out tight, it will stay sync'd as the engine grows with temp.
The size of the pulleys (or at least the input pulley) has to work with the throw of the gas pedal.
I recently made a new pulley for my 914 (CIS setup) to replace a plastic one I made a couple years ago that was starting to deteriorate(looked ugly anyway)...
1.625" OD with a ~.150" cut (1.470 dia at groove) worked with a 914 pedal, IIRC a bug may need slightly smaller or you might not get WOT. The 914 setup is somewhat adjustable at the pedal end.
I made my pulleys up from 3/8" flat stock, and used 10/32 screws for cable clamps this time around. Would be easy to put 2 grooves in 3/8"...
As long as the carb-to-carb cable/sheath isn't stretched out tight, it will stay sync'd as the engine grows with temp.
The size of the pulleys (or at least the input pulley) has to work with the throw of the gas pedal.
I recently made a new pulley for my 914 (CIS setup) to replace a plastic one I made a couple years ago that was starting to deteriorate(looked ugly anyway)...
1.625" OD with a ~.150" cut (1.470 dia at groove) worked with a 914 pedal, IIRC a bug may need slightly smaller or you might not get WOT. The 914 setup is somewhat adjustable at the pedal end.
I made my pulleys up from 3/8" flat stock, and used 10/32 screws for cable clamps this time around. Would be easy to put 2 grooves in 3/8"...
Addendum to Newtons first law:
zero vehicles on jackstands, square gets a fresh 090 and 1911, cabby gets a blower.
EZ3.6 Vanagon after that.(mounted, needs everything finished) then Creamsicle.
zero vehicles on jackstands, square gets a fresh 090 and 1911, cabby gets a blower.
EZ3.6 Vanagon after that.(mounted, needs everything finished) then Creamsicle.
- Class 11 streeter
- Posts: 4083
- Joined: Sun Nov 11, 2001 12:01 am
- slowtwitch
- Posts: 533
- Joined: Mon Nov 08, 2004 9:38 am
- Piledriver
- Moderator
- Posts: 22771
- Joined: Sat Feb 16, 2002 12:01 am
For the low budget inclined, my hacked together, scrap steel angle-iron/sawzall and battery powered drill made setup set me back ~$6, made the pulleys at work for "training" purposes
Bicycle brake cable works fine greased up with CV joint grease.
Teflon jacketed stuff might have driven the price up to ~$20.
The only reason I retired mine (after several years and ~50+K miles) was due to ditching the Webers entirely and going to a single TB. (CIS) and tat was NOT driven by the linkage in any way. I think I only had to adjust sync once, and that was when I got my Snail and could do it right.
If/when I go to ITBs again, it will have a split cable setup.

Bicycle brake cable works fine greased up with CV joint grease.
Teflon jacketed stuff might have driven the price up to ~$20.
The only reason I retired mine (after several years and ~50+K miles) was due to ditching the Webers entirely and going to a single TB. (CIS) and tat was NOT driven by the linkage in any way. I think I only had to adjust sync once, and that was when I got my Snail and could do it right.
If/when I go to ITBs again, it will have a split cable setup.
Addendum to Newtons first law:
zero vehicles on jackstands, square gets a fresh 090 and 1911, cabby gets a blower.
EZ3.6 Vanagon after that.(mounted, needs everything finished) then Creamsicle.
zero vehicles on jackstands, square gets a fresh 090 and 1911, cabby gets a blower.
EZ3.6 Vanagon after that.(mounted, needs everything finished) then Creamsicle.
-
- Posts: 824
- Joined: Mon Jul 24, 2000 12:01 am
I think it can be a lot simpler than what y'all are doing. Look at an 80's BMW R-series (boxer twin) motorcyle throttle cable. It's one cable length from the throttle then splits into a Y for two cables out to either carburetor. There are cable length adjustments both at the split and at the ends. Once the carbs are synched those cables don't go out of adjustment. You'd need to fab would be the cable stay on the carburetor, nothing else. Those old beemers stay in tune.
- Piledriver
- Moderator
- Posts: 22771
- Joined: Sat Feb 16, 2002 12:01 am
That's pretty much exactly what I did, I used a motorcycle cable splitter & ends (used Wal-Mart procured bicycle cable and ends, actually), thus the title of the thread...Paul Illick wrote:I think it can be a lot simpler than what y'all are doing. Look at an 80's BMW R-series (boxer twin) motorcyle throttle cable. It's one cable length from the throttle then splits into a Y for two cables out to either carburetor. There are cable length adjustments both at the split and at the ends. Once the carbs are synched those cables don't go out of adjustment. You'd need to fab would be the cable stay on the carburetor, nothing else. Those old beemers stay in tune.
The 3 pulley setup does have packaging advantages for (at least) upright cooling though, as tight 90 degree turns are not really suited to a cable pull setup.
Slowtwitches latest version only had 2 pulleys, which by my reckoning is as minimalist as the laws of mechanics allow on a dual carb setup, and probably has a lower parts count than ~any other setup I can imagine.
The main difference vs most motorcycle apps is due to the rotation of the throttle shafts, and the pulleys make for an easy and precise method of doing that, (most motorcycles with shaft throttles DO use pulleys, or at least a section of one)
... as well as providing a ~zero stress connection at the carb end
As I and likely Slowtwitch implemented the cable clamps, even under the clamp screw, it doesn't fray, as it's clamped in a groove, not smashed flat.
The first version I did (Not pictured) used a lever pull setup on the carb end... It worked OK too, but I think the pulleys were better anyway for several reasons previously mentioned.
I needed to make SOMETHING anyway, as the original setup got ... lost .., due to having a CB Hexbar on it for a few months in the interim, mistakenly purchased as it LOOKED better engineered than what I made in my driveway with junk I had laying around in an hour or 2, while drinking beer.
... I absolutely despise the hexbar things now.
Thanks for the vote of confidence in the basic cable pull design though!
If produced in decent quantities, this could be less expensive than most>all other linkage designs, very likely more flexible, and almost certainly better than ANY of them in any way that matters. (Note pretty much all modern production vehicles (that aren't the OTHER sort of "throttle-by-wire"

Addendum to Newtons first law:
zero vehicles on jackstands, square gets a fresh 090 and 1911, cabby gets a blower.
EZ3.6 Vanagon after that.(mounted, needs everything finished) then Creamsicle.
zero vehicles on jackstands, square gets a fresh 090 and 1911, cabby gets a blower.
EZ3.6 Vanagon after that.(mounted, needs everything finished) then Creamsicle.
- Type 4 Unleashed
- Moderator
- Posts: 2202
- Joined: Tue Nov 08, 2005 10:43 pm
Here is Marks pulley & cable setup. The throttle cable to the box that pulls 4 cables in turn pulls 4 pullies. 1150R 45mm BMW TB's with adaptor plates to bolt to IDf manifolds.
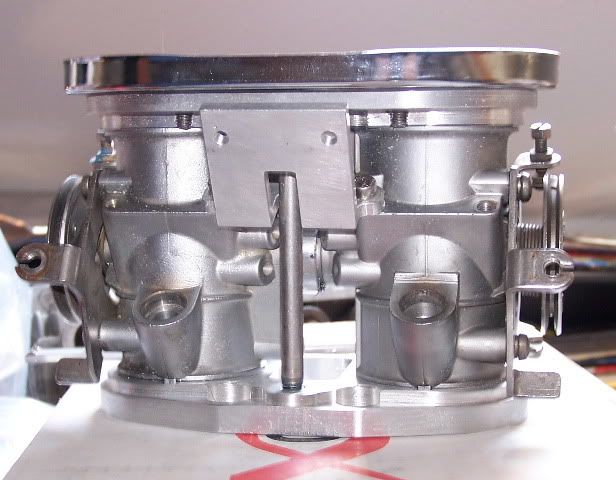
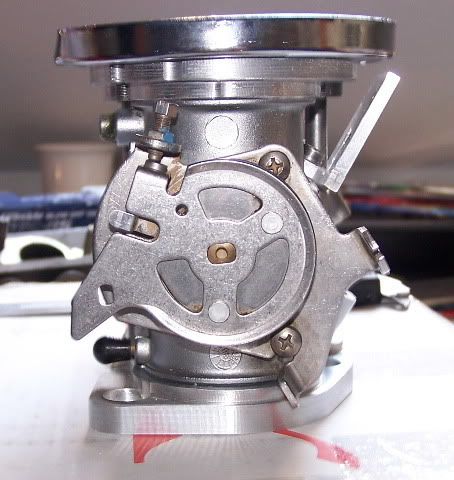
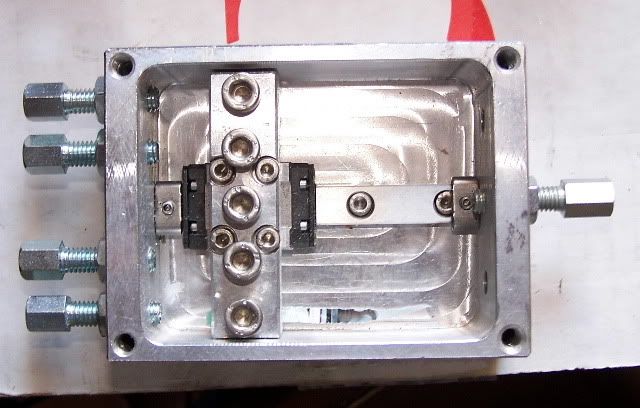
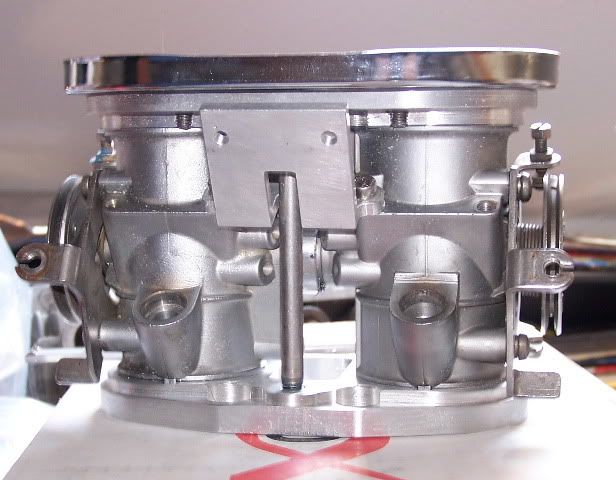
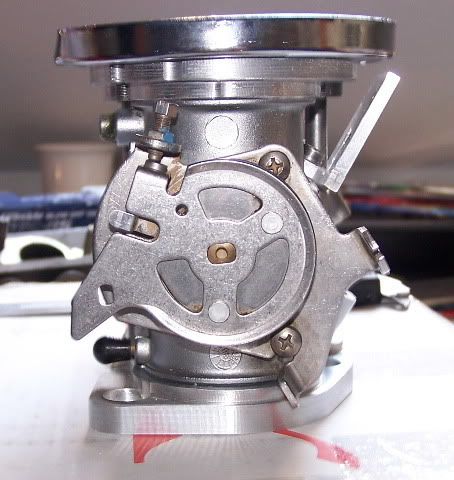
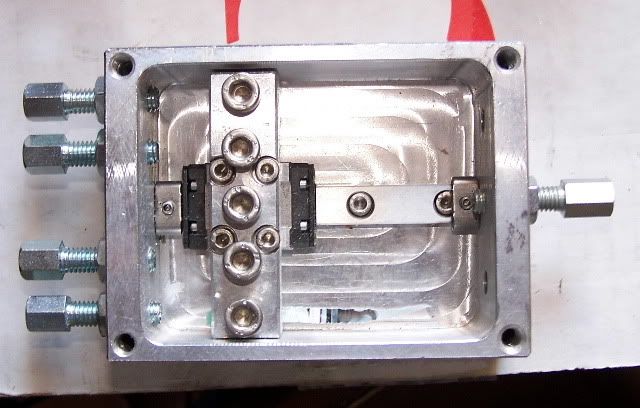
Richard
EMW
“Have you ever noticed how some people never
have the money to do it right, but can always
find the money to do it twice ?”
EMW
“Have you ever noticed how some people never
have the money to do it right, but can always
find the money to do it twice ?”