
This is a long post, but worth it.
The stock VW Type 1 crankcase breather can't handle racing pressure. The engine comes with a single crankcase breather on the oil filler tower so small you can't stick the tip of your finger into it. Four cylinder Porsche 356 and 912 engines were a little better, evolving through the years from vents on the valve covers, to hoses coming off the heads and the oil filler tower to the carb intakes, just barely enough for light competition.
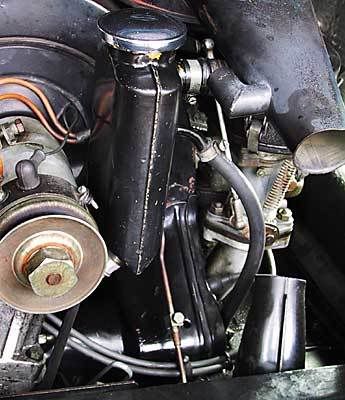
High performance engines create a storm of high internal crankcase pressure as the crankshaft spins, and the pistons fly back and forth. Add some piston ring blow-by, and power goes down as pressure resistance to the moving parts go up. Reliability also drops as oil blows out of seals, gaskets, and even the engine's crankcase breather.
Racers of all types resort to "dump cans," a can or tank the crankcase breather vents into, keeping oil off the track. At screaming win-or-break RPM's, air pressure is forcing oil out of every hole in the engine it can find.
What Causes Crankcase Pressure?
Two things. Moving parts, and piston ring blow-by. The "pressure" we talk about is made up of air resistance, and splashed oil droplets suspended in gases that made it past the piston rings, including unburned gasoline and water vapors.
Pistons push air and gasses on both ends of the cylinder. Moving anything takes energy. Pumping pressure out of an engine through a small breather also takes energy, because the breather hole is so restrictive.
When crankcase pressure builds because the air and gasses inside can't easily vent, it will escape wherever it can. This is the cause of many small oil leaks.
To fix this, you have to exhaust the area inside the crankcase, removing the combustion products, which blow by the piston rings. After only a couple of power strokes the case pressure rises. The perfect breather would expel crankcase pressure and blow-by gas while simultaneously providing low pressure inside the crankcase.
How Much Pressure Is In A Crankcase?
A vacuum/pressure gauge connected to a port into the engine (not the intake, but the crankcase itself) will show you how much pressure your engine creates as it runs. Most engines don't have a handy crankcase vacuum port, but sometimes an oil dipstick hole can be a good improvised location.
A rough rule of thumb is that for every one litre of engine displacement, it will blow out (by volume) about 1.25 cubic feet per minute of air at high (5000+) rpm.
That means that even on a modest 2-litre engine turning six grand, you can have 2.5cfm trying to blow out, at 30psi (or more) of internal pressure.
Air-Cooled VW and Porsche Engine Breather Problems To Overcome
The VW Type 1 engine breathing system changed very little from the old 1100cc's to the 1600's. VW provided a half-inch diameter vent hole on top of the generator stand near the oil filler cap. A tube ran from the vent hole to the air cleaner, providing a low-pressure path for the vented gasses to follow to the intake.
That small hole was okay in 1949, but became increasingly more marginal as horsepower and RPM's went up. And VW never improved it.
The only venting changes were the clean-air mandated elimination of the "condenser tube" that ran downwards from the oil filler housing atop the generator stand, to allow drip-off of condensed water and oil contaminants.
A problem the VW (and VW-derived Porsche 356) engine has is oil being sprayed by the spinning cam gear, which is just in the right place to constantly flood the generator stand. VW compensated for this with a louvered splash plate between the case and generator stand. With no splash plate, a VW engine running without an oil cap would blow oil out the filler hole like a fountain.
Porsche's spray problem was not as bad, because the 3-piece 356 case enclosed the cam gear in a separate front cover housing with a cast-in deflector above the cam, blocking most of the cam gear spray.
This oil spray in the VW and Porsche significantly adds to the oil vapor and droplets in the crankcase, making the crank assembly rotational resistance even greater, and the need to improve case venting even more important.
"Sucked-In" Valve Cover Gaskets
VW Type 1 and Type 4 engines, and Porsche 356 people have all experienced valve cover gaskets that appear to have "sucked in," causing oil leaks. This seems to indicate low pressure, not high, inside the crankcase.
The gaskets have indeed been sucked in, and low pressure in the head was the problem, but as a side effect of very high pressure elsewhere in the engine.
Pressure highs move about inside the engine, displaced from one area to another by the pistons. There is an instant in which the heads contain very high crankcase pressure, then another in which it is very low. Due to the way VW and Porsche valve covers fit their gaskets, the gaskets can't be forced outward as easily as they can be sucked in, so sucked-in wins.
Porsche engineers tried different venting methods on racing 356 valve covers, to help out the small generator stand vent that even the early 356 engines had. One try was to design vents directly on the top center of the valve covers. These were raised openings covered by metal filter mesh, but oil tended to blow out past the mesh and soak the outside of the valve covers.
Racers sometimes rigged vent hoses directly off the valve covers, routed to dump cans. These reduced crankcase pressure, but the problem was the valve covers had to be removed a lot. Having to always disconnect the hoses was extra work, not to mention the cause of oil leaks if the frequently disconnected hoses loosened or came off accidentally.
Porsche finally refined its system (in the 912) to hoses that came directly off the heads, not the valve covers, each head venting to its individual cylinder bank carburetor air cleaner.
So Why Not Just Run a Bigger Breather?
While the total interior volume of the crankcase remains constant as one piston goes up while another goes down, the displaced air has to move back and forth in the case. You suffer power losses from this.
A too-small crankcase breather (relative to crankcase volume and rpm) will not allow enough equalization between pistons strokes to make much difference.
The old school racer's fix, motorcycle to race car, was to fit (if possible) a big, open breather pipe, and let the case suck in and blow out air as the engine runs. There is no power loss with this system as long as the breather is big enough, so that no significant pressure difference builds up between the crankcase and the outside atmosphere.
But the problem with this is there is usually no easy place to put such a big hole.
So, what then must we do? Another post follows.